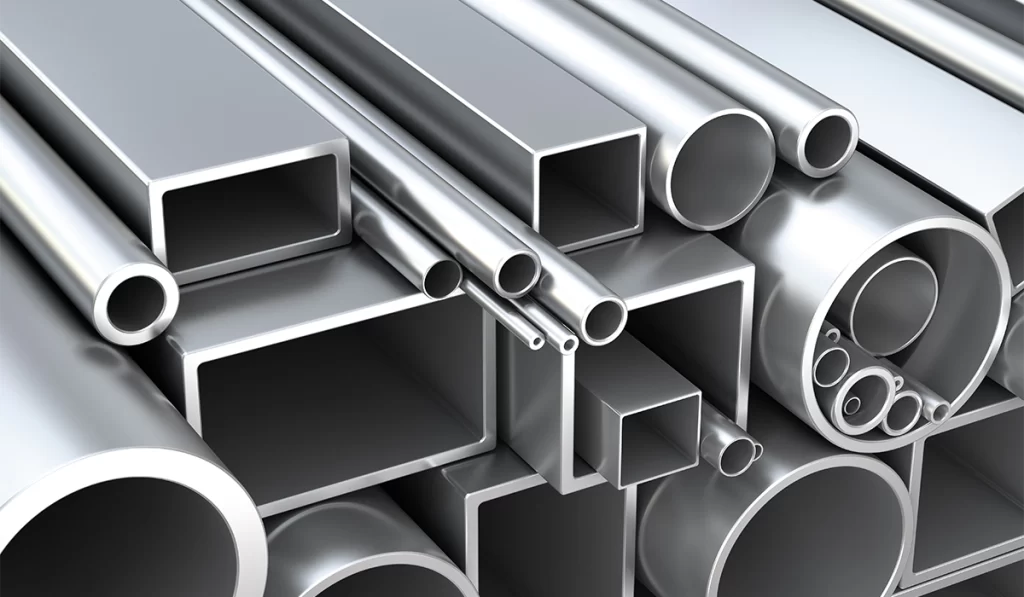
Stainless Steel Pipe Manufacturers, Carbon Steel Pipe Manufacturer, Alloys Steel Pipes Manufacturer, Stainless Steel Seamless Pipe supplier,
Stainless Steel Pipes, Carbon Steel Pipes, Alloys Steel Pipes, Mild Steel Pipes and Many More Grade Pipes As per Client Requirement.Pentagon Steel India is a leading Stockist, Supplier and Exporter of All Grade of Steel Pipes in India. Pipes are Hollow Cylindrical Tubes that have been used by humans for thousands of years for a variety of purposes. Pipes can be made from nearly any material however because the current definition of Pipes entails more than just Hollow Tubes that transmit Fluid, Metals have grown more prevalent in Pipe Fabrication. Steel Pipes as a metal alloy have a wide range of Mechanical and Chemical Properties that may be used in even the harshest conditions. As a result, Steel Pipes are now used in a number of applications for Transportation, Manufacturing and Structural Purposes. Steel Pipes can be made from a variety of Steel Grades and Production Methods, which vary depending on the application.
What is a Steel Pipe?
Steel Pipes are large Hollow Tubes that are utilized in a number of settings. Pipes are the most widely utilized product Manufactured by the Steel Industry due to their versatility. They are often utilized to transport both Fluid and Solid Particles. Because of their tremendous strength, they can also be used in subsurface Water and Gas Transit across cities, as well as in Construction for Heating, Plumbing and Other Functions. People have been Using and Manufacturing Pipes for various purposes for thousands of years.
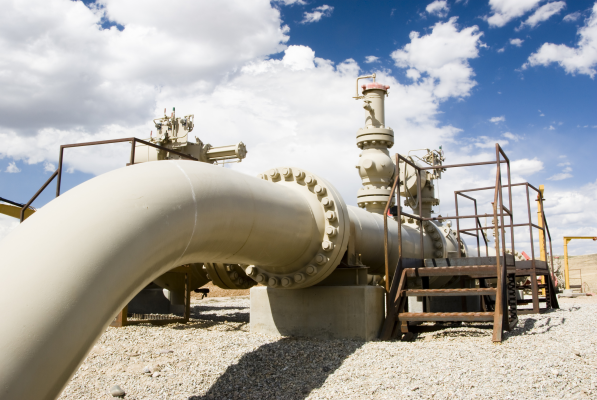
How is Pipe used?
Pipes are used in Infrastructure, Transportation and Industry. Different Materials, Design Qualities and Manufacturing methods for Steel Pipes have been developing and varied according to the application.
Steel Types Used in Pipes
Stainless Steels:
Stainless Steel, often classified as Alloyed Steel primarily contains Chromium as the key Alloying Element ranging from 10 to 20% by Weight. The main purpose of adding Chromium is to make the Steel Resistant to Corrosion giving it its “Stainless” Quality. Stainless Steel Pipes are widely used in challenging environments where both Corrosion Resistance and High Strength are essential such as in Marine, Medical, Water Purification and Oil & Gas Industries. Common Grades for Pipe Manufacturing include 304/304L and 316/316L. The 304 grade is known for its Excellent Corrosion Resistance and Strength while the 316 Series though offering slightly Reduced Strength has Superior Welding Capabilities.
Carbon Steels:
Carbon Steels account for around 90% of all Steel Pipe production. They contain fewer alloying elements and perform poorly in harsh environments when used on their own. Despite this Carbon Steel are often chosen for lower-stress applications due to their lower cost, adequate Mechanical Properties and Good Machinability. However they are less suitable for High-Pressure conditions and extreme environments. Carbon Steel Pipes are commonly used in the Automotive and Marine industries, as well as for Oil & Gas Transportation. Grades such as A500, A53, A106 and A252 can be found in both Seamed and Seamless forms.
Alloyed Steels:
The addition of Alloying elements like Nickel, Chromium, Manganese and Copper enhances the Mechanical Properties of Alloy Steels making them more resistant to stress and high-pressure applications. These elements which can range from 1% to 50% by Weight, impart various Mechanical and Chemical qualities depending on the composition. Alloyed Steel Pipes are typically used in demanding conditions such as the Oil and Gas Industry, Petrochemical Plants, Refineries and Chemical Factories where durability is crucial.
Galvanized Steels:
Galvanized Steel Pipes are coated with Zinc to protect against Corrosion. This Zinc Layer shields Pipe from corrosive elements that can damage the Steel. While Galvanized Pipes were once the standard for Water Supply Lines, they are now less commonly used due to the Labor-Intensive Process of Cutting, Threading and Installing them. However, they are still used in large-scale commercial applications. These Pipes come in Sizes ranging from 12 MM (0.5 Inches) to 15 CM (6 Inches) and are typically available in 6-Meter (20-Foot) Lengths. One drawback is their relatively short lifespan of 40 to 50 years. Despite the protective Zinc Coating the inside of the Pipe may corrode over time, especially if it carries corrosive substances. Therefore, regular monitoring and upgrades are essential.
Design parameters:
There are two types of Pipes: Seamless and Welded Seam and they serve various purposes. Seamless Pipes are generally Thinner and Lighter hence, they are most commonly employed in Bicycle Manufacturing and Fluid Transport. Seamed Pipes are Heavier and Stiffer resulting in superior consistency and longevity. Pipes used for Gas Transportation, Electrical Conduit and Plumbing are typically Seamed. Several parameters should be regulated during production to ensure that the application’s requirements are met. A Pipe’s Diameter for example is built with its intended usage in mind. Smaller-Diameter pipes may be used for Hypodermic Needles while Larger-Diameter Pipes may be utilized for Urban Transportation. Wall Thickness is another key element to consider because it directly influences the Pipe’s Strength and Flexibility. Other modifiable characteristics include Length, Coating and End Finish all of which are related to one another.
Types of Pipes:
Pipes can be categorized into two main types based on their manufacturing process: Seamless and Seamed Pipes.
Seamless Pipes:
Seamless Pipes are produced through a complex process that involves Drilling Hollows from Billets followed by Cold Drawing and Rolling. Controlling the Outer Diameter and Wall Thickness of Seamless Pipes is more challenging compared to Welded Pipes, but the Cold-Working Process improves the Mechanical Properties and Tolerances. One of the primary advantages of Seamless Pipes is that they can be Manufactured with Thicker Walls, offering better Mechanical Properties and Corrosion Resistance due to the absence of a Weld Seam. These Pipes are often chosen for extreme environments involving Heavy Loads, High Pressure or Corrosive Conditions.
Seamed Pipes:
Seamed or Welded Pipes are made by Rolling a Steel Plate into a Tubular Shape and Welding along the Seam. Depending on the Pipe’s dimensions and intended use, the Welding may be Straight Seam or a Spiral Seam. While Welded Pipes generally have finer Tolerances and Thinner walls compared to Seamless Pipes, they are more affordable and have shorter lead times. However, the Weld Seam is a potential weak point where cracks could develop, making it important to carefully monitor surface finishes both Inside and Outside the Pipe during production. Despite this, Seamed Pipes are often preferred for cost-sensitive applications.
The Manufacturing of Steel Pipes generally follows two primary methods: Seamless and Seamed.
Each process starts by Casting Raw Steel into a more usable form, either as a Hot billet or a Flat Strip. These are then either stretched into Seamless Pipes or Welded along the edges to create a Seamed Pipe.
Mandrel Mill Process (Seamless Pipes):
In the Mandrel Mill Process, a Solid Round Steel Billet is used. The Billet is Heated in a Rotary Hearth Furnace and a hole is punched at one end. The Billet is then processed through Rotary Piercing where it’s Rolled between two Barrel-Shaped Rolls at high speed. As the Billet is Rolled a Pipe shell forms around a Water-Cooled Piercer Point. The Pierced Pipe shell is passed through a Floating Mandrel Mill which uses Multiple Rolls and Mandrel Bars to further Shape and Size the Pipe. After Reheating the final Rolling Stage completes the desired Dimensions with High-Pressure Water descale removing the iron-oxide scale from the Pipe surface.
Mannesmann Plug Mill Process (Seamless Pipes):
This process also starts with a Round Billet but it differs from the Mandrel Mill in that it uses a Rolling Plug instead of a Mandrel. The Billet is Rolled between Conical Rolls that operate against the Material’s Flow Direction. The process shapes the Hollow Pipe shell to the required Wall Thickness using a series of Rolling and Smoothing Passes.
Extrusion (Seamless Pipes):
In Extrusion a heated Steel Billet is forced through a Die with a Mandrel attached to the Dummy Block which creates a Hollow Tube. The ram forces the material to flow between the Die and the Mandrel forming the Pipe.
Seamed Pipe Manufacturing
Seamed Pipes are produced by Welding the edges of Flat Steel Plates or Strips. This process typically involves forming the Flat Material into a circular shape using a Roller or Bending Machine and then Welding it. The most common methods for Welding include:
Electric Resistance Welding (ERW):
Flat Steel is formed into a Cylindrical Shape and Electric current is applied to Heat and Weld the edges.
There are two types of ERW:
High-Frequency Induction Welding (where current is Induced via Magnetic Fields) and High-Frequency contact Welding (where current is applied directly through contacts). ERW is preferred for Large-Diameter and Thick-Walled Pipes.
Electric Fusion Welding (EFW):
This process uses Electron Beams to Weld Steel Plates. The high kinetic energy of the Electron Beam is converted into Heat, Melting the workpiece and forming a Seam.
Submerged Arc Welding (SAW):
Here an Electric Arc is formed between a Wire Electrode and the Workpiece while Flux creates protective Gases and Slag. SAW can be Longitudinal or Spiral with Longitudinal Welding creating U-Shaped Seams and Spiral Welding producing Helical Seams.
Quality Control :
Various measures are used to ensure Pipes meet Specifications including X-Ray Gauges to check Thickness and Hydrostatic Testing which involves filling the Pipe with water and applying pressure to detect defects.
Specifications and Standards:
Steel Pipes are defined by Nominal Pipe Size (NPS) with the External Diameter remaining constant while the Wall Thickness and Internal Diameter varies based on the Pipe Schedule. Common standards include:
ASME SA106 Grade B: Seamless Carbon Steel Pipes for High-Temperature service.
ASTM A312: Seamless and Welded Austenitic Stainless-Steel Pipes.
ASTM A36: Carbon Steel Pipes for Structural or Low-Pressure use.
These standards typically involve Testing for Chemical Composition and Mechanical Properties to ensure Quality.
Structured Use:
Structural use is most usually associated with Building and Construction with Steel Tubes serving as the Building Material of choice. Steel Tubes are utilized to lend strength and stability to very Tall Buildings or Structures. End-Bearing Piles and Friction Piles are two forms of Steel Pipes used in Structural Applications both of which aim to transfer the load of the building. In certain situations, Steel Pipes are pushed deeply into the Earth before the foundation is erected providing significant support to the building especially when the ground is unstable. Scaffolding Poles are another structural application of Steel Pipes allowing Construction Workers to access previously inaccessible regions of the building. They are Constructed by joining Steel Tubes together to form a cage that surrounds the building.
Manufacturing Usage:
Steel Pipes are used for a variety of Manufacturing Purposes. Guardrails are a popular way to offer safety for Staircases and Balconies, as well as for Bicycles and Pedestrians on the street. Steel Pipes can also be used as security bollards which are intended to block off an area from Vehicular Traffic in order to Safeguard People, Buildings or Infrastructure. Steel Pipes can also be used to adorn outdoor spaces. Many commercial Bike Racks are made by bending Steel Tubes. Steel is extremely durable and strong making it resistant to theft.
Transportation Usage:
Steel Pipes are most commonly used for product transportation since their Raw Material properties make them ideal for long-term installations. As previously stated, different applications demand different attributes for low-pressure applications, a Steel Pipe is not anticipated to demonstrate ultra-high strength because it is not subjected to severe force. More specialized uses in the Oil and Gas Industry may necessitate more severe criteria due to the product’s hazardous nature and the risk of increased pressure. These requirements increase the cost, making quality control more vital.